Leak Rates Explained
In leak testing, there is no one method that works best for every situation. Commonly used leak test methods vary in the cost of the equipment, the cycle speed of the test method, and the output and accuracy of each test method.
Bubble leak testing is the simplest and least expensive method of detecting leaks. However, bubble leak testing is often too time consuming, or lacks the accuracy needed of many common applications. The chart below provides comparative reference between the leak rates that are achievable with more costly, yet more accurate and timely methods vs the time needed for a test bubble to escape to atmosphere from a bubble leak test (the bubble being 2 mm in size, similar to a bubble you would see in a glass of champagne).
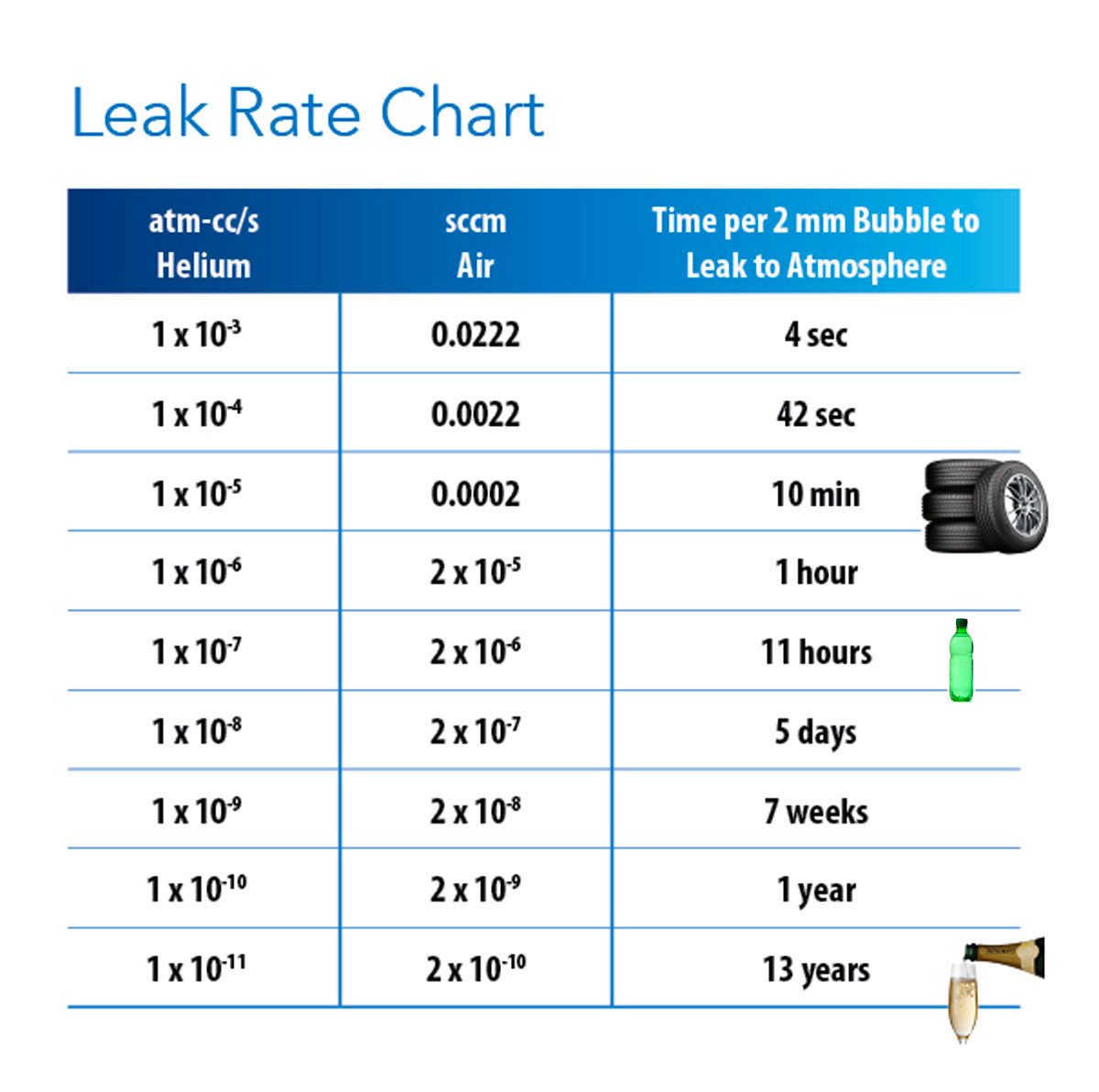
For example, most tires are tested to 1x10-5 atm-cc/s, units commonly seen from a high vacuum helium leak detector. On an air pressure decay style leak detector, the equivalent leak rate would typically be stated as 0.0002 sccm. And a bubble leak test would take 10 minutes before the first bubble would escape to atmosphere.
Comparatively, a molded plastic soda bottle requires meeting a 1x10-7 or lower leak rate in order to achieve the desired shelf life of a bottled beverage. A bubble leak test would require an 11-hour test—not a practical solution. But a pressure decay style leak detector, while more expensive, will accurately accomplish a test of that leak rate and at speeds required of the high speed process.
Finally, while extremely costly, high vacuum leak detectors, that often incorporate Clippard EV valves, are capable of testing for leaks as low as 1x10-11 atm-cc/s, a test equivalent to waiting 13 years before seeing the first 2 mm bubble escape to atmosphere.
See this Overview of Leak Detection Testing article to learn more about common methods used by Clippard in the validation and testing of product.
Related Content
- An Overview of Leak Detection Testing
- Optimizing & Improving Leak Detection Systems
- Pneumatic Solutions for Leak Testing
- Video: How a Basic Leak Decay Tester Works